Industrial Hardware and Machine Parts
JUNKER grinding machine: Maximum precision
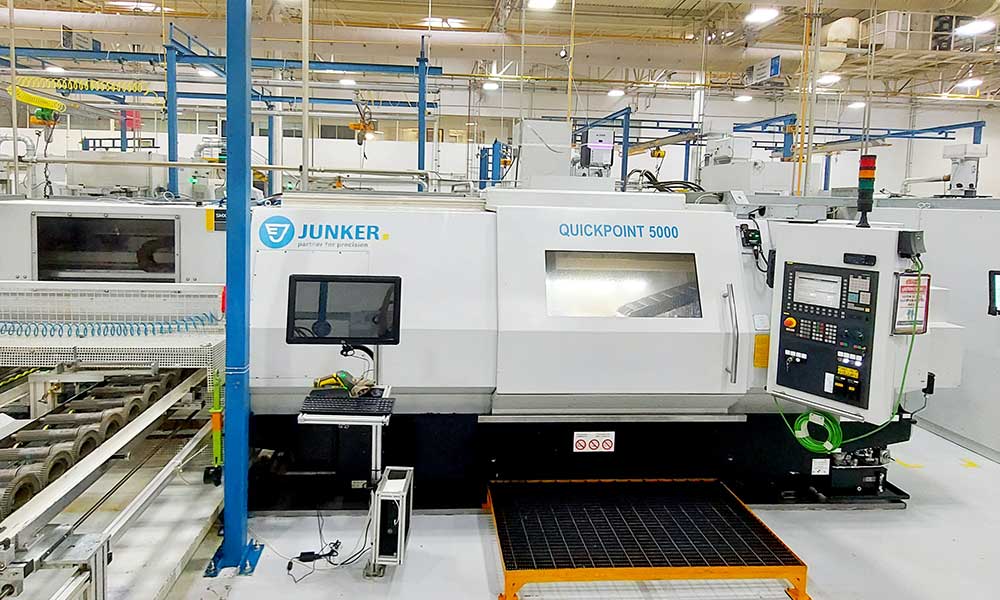
The QUICKPOINT cylindrical grinding machine from JUNKER impresses with its enormous capacity and flexibility through a single clamping process. Sisamex produces gear shafts with maximum precision while reducing auxiliary process times; this ensures an effective production with low handling costs.
Sisamex processes an average of 160,000 gear shafts per year in Mexico with the QUICKPOINT high-speed grinding machines.Francisco Vélez García, the person responsible for processes at Sisamex, confirms: “This machine unites precision and maximum flexibility, as the cylindrical grinding machine is versatile in use and has an enormous capacity.” The production facility is located in Cd. Gral. Escobedo, N.L., one of the largest industrial centers in Mexico.
A single clamping process
One of the outstanding technical advantages is the grinding of the gear shaft in a single clamping process. Sisamex invests in an economic grinding process that saves time and money. The gear shaft is clamped between centers for processing the outer diameters and end faces. The CNC tailstock withdraws for processing of the inner cone, with the gear shaft being held and guided by the steady rest. The industrial company processes different gear shaft workpiece families on QUICKPOINT, showcasing the JUNKER grinding machine’s versatility. Mr. Vélez García explains: “Various workpiece types are swapped several times a day. We can flexibly retool the grinding machine without complications and in the shortest possible time. The temperature in the plant is controlled at 23 to 26 °C. This ensures a stable grinding process with the in-process measuring systems used by JUNKER. A high process capability (CpK) is achieved by the use of the JUNKER grinding machine.”
A high process capability (CpK) is achieved by the use of the JUNKER grinding machine
Sisamex gear shafts
The highly precise gear shaft is built into powerful trucks. (Source: Sisamex)
The grinding machine is equipped with an internal loading gantry for loading and unloading. Switching to new workpiece types on a QUICKPOINT is possible at low costs – and this in turn reduces auxiliary process times to a minimum.
With JUNKER’s grinding machine, we have reduced production costs and optimized the grinding process
Saving time and money with JUNKER services
“The QUICKPOINT grinding machine is the heart of production, which is why fast service is very important to us. It was possible to significantly reduce downtimes with JUNKER’s technical support,” says Mr. Vélez García.The installed components of the grinding machine are customized, variable, and of the highest quality. Using them saves JUNKER additional maintenance costs. Mr. Vélez García adds: “With JUNKER’s grinding machine, we have reduced production costs and optimized the grinding process.”
The cooperative business relationship has existed since 2012. Sisamex employs committed grinding experts with unbelievable technological expertise. This connects both companies and makes planning, processing, and later implementation easy.
It was possible to significantly reduce downtimes with JUNKER’s technical support
Internal cylindrical grinding
Precisely processed internal end faces of the gear shaft. (Source: SISAMEX)
Cylindrical grinding
With cylindrical grinding, the workpieces are clamped between centers or in a clamping chuck. (Source: JUNKER)
Flexible high-performance grinding machine
QUICKPOINT standard operations are shoulders, outer diameters, cones, chamfers and recesses. (Source: JUNKER)
Internal cylindrical grinding
Internal cylindrical grinding enables the precise processing of internal functional surfaces, such as drill holes, cones or end faces. (Source: JUNKER)
-
Industrial Hardware and Machine Parts8 years ago
The necessity of bolted flange connection training
-
Drive systems6 years ago
Intelligent frequency inverters for digital production
-
Motors8 years ago
New generation of hollow shaft motors
-
Industrial Hardware and Machine Parts8 years ago
ABB and Formula E partner to write the future of e-mobility
-
Industrial Hardware and Machine Parts8 years ago
Rexnord adds to its Autogard Torque Limiters with the XG Series
-
Motors8 years ago
ZF Technology on the Winners’ Podium of the Dakar Rally 2017
-
Gear drives7 years ago
Klingelnberg at control 2018: Tactile and optical measurement on one machine
-
Motors8 years ago
Get a first-class ticket to productivity
-
Motion control7 years ago
Where the robots come from?
-
Motion control8 years ago
Rexnord to Acquire Centa Power Transmission
-
POWER TRANSMISSION TECHNOLOGIES5 years ago
EUROTRANS Board meets for its first session in 2021
-
Industrial Hardware and Machine Parts9 years ago
Custom hobbing tool enables 45-degree angles