Chain and Chain Drives
Why should you be asking questions?
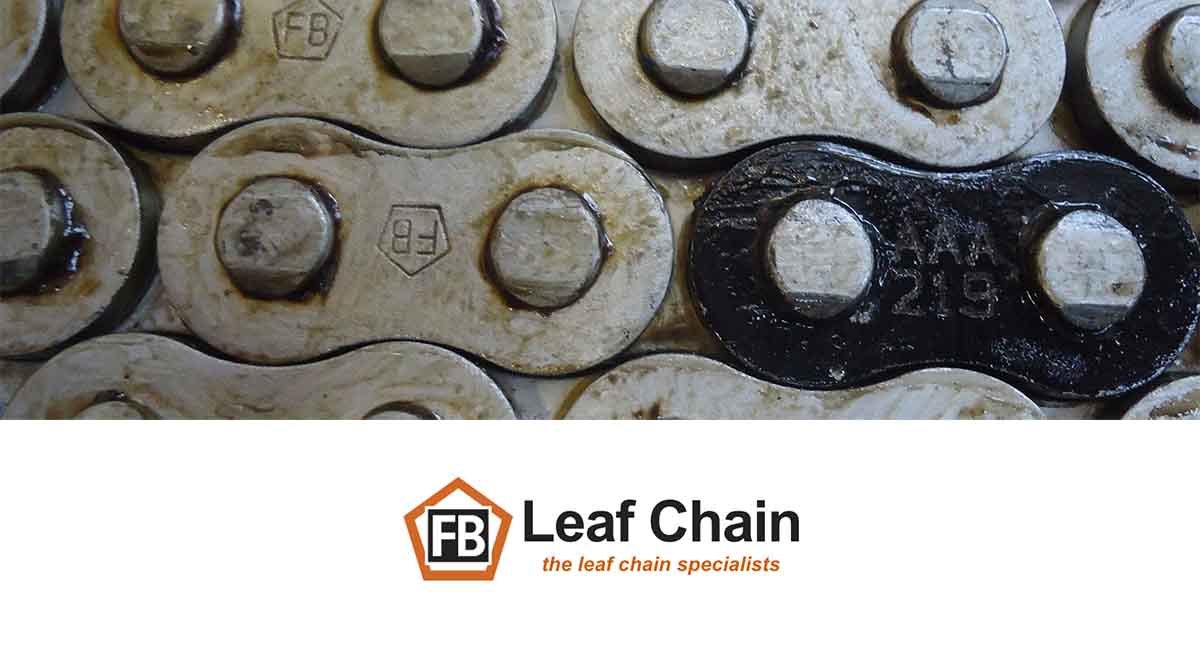
Not all corrosion-resistant leaf chain is created equal, so it’s vital to question your supplier thoroughly to ensure you get the optimal product for the job.
When standard leaf chain is fitted to materials handling equipment, such as forklifts or telehandlers, that is repeatedly being cleaned to meet hygiene standards or used outside on roads or in yards, there is a strong chance its operating life is being reduced by corrosion. Fitting a special corrosion-resistant leaf chain can bring about major improvements in service life, as well as the total cost of ownership and operation, so it’s important to get the right one.
1. What makes corrosion resistant chain?
There are several different types of chain marketed as being corrosion resistant chain. One of them is stainless-steel leaf chain, which although offers good resistance, only has one eighth of the tensile strength of standard leaf chain, so you would need a much larger chain to safely lift the same load. Another type is zinc plated leaf chain, which unfortunately comes with a risk of hydrogen embrittlement from the plating process. This weakens and fractures the material. We would not advise customers to use either of these leaf chain types. Instead, we recommend zinc flake coated leaf chain, which has the same tensile strength as standard leaf chain and no risk of hydrogen embrittlement and fracturing.
2. How long does it resist corrosion in a salt spray test?
It is virtually impossible to compare leaf chain performance in industrial environments over long periods but the controlled conditions of a 5% neutral salt spray test according to the ASTM B117 standard give a good indication. Within these parameters, FB zinc flake coated leaf chain regularly lasts up to 800 hours before showing any signs of corrosion, which should serve as a benchmark for comparing the resistance of chains from other suppliers.
3. Has the chain’s tensile strength been impacted by the processing temperature?
The mechanical properties of the steel used for leaf chain components are altered through heat treatment. When the coating is baked on, it can anneal the material and reduce the leaf chain’s strength. The lower temperature of the FB coating process means that the tensile strength of the chain remains the same as our standard leaf chain, which is at least 20% higher than required by the ISO standard.
4. Are the links coated before assembly?
Coating the links before assembly is essential as it ensures each link has been completely and consistently covered for increased corrosion resistance. When we implemented this process to our zinc flake coated leaf chain in 2016, we found its performance in salt spray tests jumped from 500 to 800 hours.
5. What environmental impact does the coating have?
Some zinc flake coatings contain hexavalent chromium, which although an effective defence against corrosion, is carcinogenic and poses a risk both to people’s health and the environment. Since 2012, we have been using a water-based coating, which complies with the EU End of Life Vehicles (ELV) Directive and the Restriction of Hazardous Substances in Electrical and Electronic Equipment (RoHS).
Taking the time to question your supplier on these points will not only ensure you get good performance from your corrosion-resistant leaf chain but also save you money.
-
Industrial Hardware and Machine Parts8 years ago
The necessity of bolted flange connection training
-
Drive systems6 years ago
Intelligent frequency inverters for digital production
-
Motors8 years ago
New generation of hollow shaft motors
-
Industrial Hardware and Machine Parts8 years ago
ABB and Formula E partner to write the future of e-mobility
-
Industrial Hardware and Machine Parts8 years ago
Rexnord adds to its Autogard Torque Limiters with the XG Series
-
Motors8 years ago
ZF Technology on the Winners’ Podium of the Dakar Rally 2017
-
Gear drives7 years ago
Klingelnberg at control 2018: Tactile and optical measurement on one machine
-
Motors8 years ago
Get a first-class ticket to productivity
-
Motion control7 years ago
Where the robots come from?
-
Motion control8 years ago
Rexnord to Acquire Centa Power Transmission
-
POWER TRANSMISSION TECHNOLOGIES5 years ago
EUROTRANS Board meets for its first session in 2021
-
Industrial Hardware and Machine Parts9 years ago
Custom hobbing tool enables 45-degree angles