Motion control
Neugart: Gearboxes for automation and robotics
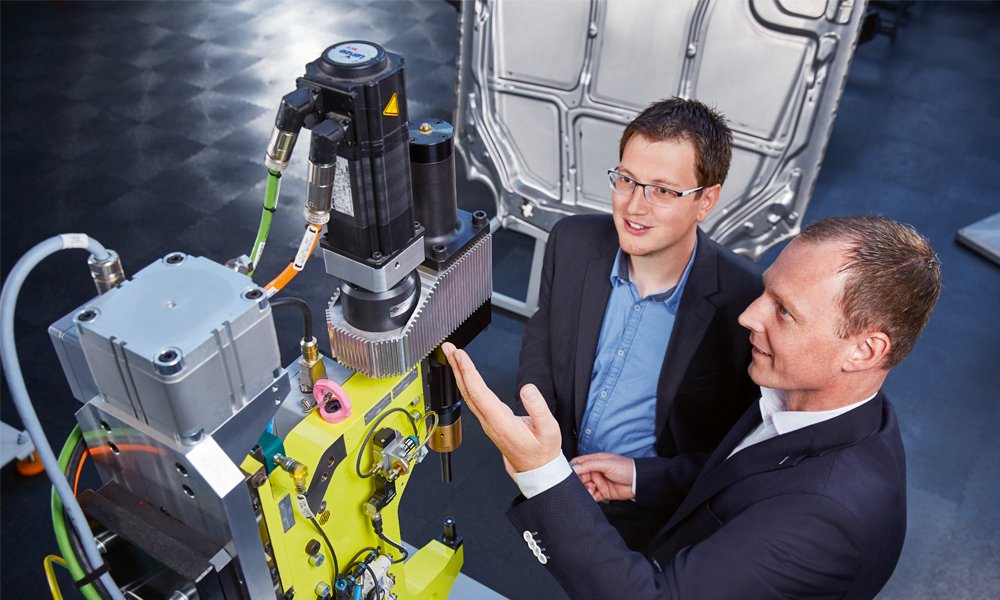
Mechanical and industrial engineers in this industry sector must maintain an incredibly difficult balancing act: delivering cost-effective products without sacrificing quality and durability. Neugart understands the difficulty of striking this balance. We understand that highly automated plants often run around the clock over the course of the whole year. Since our founding, we have been developing and producing planetary gearboxes tailored to suit these needs, constantly striving to improve our products in cooperation with our customers.
Our gearboxes strive to fulfill the most diverse requirements, depending on the type of gearbox application a client intends to use. Highly dynamic, linear handling applications demand robust, high-performance components. Thanks to the low weights of the drive components, multiple axis systems achieve a positive regulating effect and, as a result, offer more-efficient throughput times. Pick-and-place systems, on the other hand, demand high repeatability and a corresponding system rigidity that promotes fast and precise placing.
Neugart planetary gearboxes can be customized according to your requirements. They operate reliably and precisely, aiming to meet our customers’ requirements, regardless of what they may be.
Your benefits:
Cost effective gearbox solutions: Neugart planetary gearboxes use modular designs for a wide range of flexible configurations and customizations. Because of this, our customers benefit from a cost-effective acquisition price – without sacrifice to quality.
Reliable gearboxes with long lifespans: Our planetary gearboxes do not need lubricant change. Our unique design facilitates a lifetime-lubricated gearbox that performs its tasks reliably.
Smart technology for all product aspects: It’s not always simple to find the perfect gearbox for specific applications. Gearbox applications are complex and many factors will come into play during the decision process. Neugart software tools are easy to navigate and help to simplify potential questions or difficulties.
Worldwide availability: There is virtually no country in the world that does not currently use a Neugart gearbox. We have built a network of experienced sales engineers around the world so that you will always have somebody there for you — no matter your need, no matter where you are.
“We have relied on Neugart and its gearboxes for years because of the excellent advice regarding application, the high product quality and the optimally coordinated product range. In the case of our servo-clinch machine, we could not have used a better planetary gearbox.”
B.Eng. (DH) Florian Unger | Head of Development | Eckold GmbH & Co. KG
Case study: Clinching — the joining technology of the future
Florian Unger is the Head of Development at Eckold GmbH & Co. KG in St. Andreasberg, located in the Harz region of Germany. He has relied on Neugart gearbox technology for years. Mr. Unger explains, “The entire unit is easy to adjust with this gearbox manufacturer. The diverse product range provides the correct gearbox for every possible application. We have found the perfect gearbox for us here – compact, powerful, maintenance-free and at a fair price.
About the company
Eckold GmbH & Co KG is a medium-sized company founded over 80 years ago. As a manufacturer of specialized machines, the Eckhold & Co focuses specifically on joining and forming technology. They concentrate primarily on clinching, stamping and semi-tubular punch riveting technology. Company owner Gerd-Jürgen Eckold brought clinching technology onto the national market in the 1980s. Today, clinching has become indispensable in the automobile industry, household appliances and air conditioning and ventilation technology, not to mention spot welding and riveting technology. This is one of very few technological solutions available to use when different materials such as sheets of steel and aluminum need to be joined together without ancillary parts.
Task
Eckold started retrofitting and enhancing its pneumo-hydraulic clinching machines on electro-mechanical systems years ago. While both technologies remain available, there is also a clear market trend towards electro-mechanical systems. For components with different individual or total thicknesses, it is almost always necessary to adjust the base thickness in order to positively influence the undercut and stem thickness formation. A complicated matrix change is needed when using pneumo-hydraulic systems because of the fixed cylinder stroke.
With an electro-mechanical system, due to the variability of the drive stroke, the user is typically no longer reliant on a matrix change, which is more flexibly positioned in the electro-mechanical system. Other advantages clearly lie in automation and the implemented continuous quality monitoring, which can be controlled in the software program.
We see examples of this in automotive applications, where clinching pliers are mounted as a complete unit on an articulated robot (known also as joint-arm robots) and operate autonomously in production lines. Creating compact units are of the utmost importance, as compact clinching unit are absolutely necessary in order to reach areas of the automobile body that are difficult to access. With the parallel design of the gearbox and the planetary roller screw, Eckold’s machines were extremely compact right from the start. A servomotor drives the planetary gearbox directly. This is connected to the planetary roller screw through the use of a belt and generates an axial movement with a high degree of pressing force. The radial force resulting from the pre-tensioning of the belt must be absorbed by the bearing technology of the planetary gearbox that is used. The requirement of the OEM’s for more compact units and the need to reduce cycle times prompted Eckold to look for alternatives on the market.
A new gearbox undergoes a strict testing procedure at Eckold during qualification. Each gearbox unit is tested in-house and must perform 10 million strokes, in order to simulate real-world use. If the gearbox passes this test, the clinching units are delivered to the OEM’s for field-testing. The devices are then returned to the factory and analyzed in detail every 2.5 million strokes. Only the units that pass this process with 100% effectiveness have a chance of making the short list.
Solution
As Eckold set out to find a new gearbox, numerous units underwent their rigorous tests and trials. Finally, after Eckold completed their search, a Neugart gearbox was chosen. The arguments for using this gearbox are noteworthy, as it offers countless benefits in comparison to previously used gearbox technology. The Neugart gearbox has extremely high efficiency of around 98%. It is about 10mm shorter, lighter and reaches a performance data that is 5 to 10% higher than previous models. This gives clinching machines two advantages: the weight reduction increases the controllability of the articulated robot and therefore also reduces the process times. Additionally, our smart unit is even more compact. With the application of a Neugart gearbox, the Eckold clinching machine is unrivaled on the market.
It was just as important to the Eckold engineers for the gearbox not to have to be re-greased during the machine cycle, even though the components were operated on a robot arm in any spatial coordinates. The customer therefore receives a drive train which can generate an axial clinching force of up to 100 kN. In addition to the technical advantages, Neugart gearboxes are a more cost-effective solution in comparison to previous gearbox models.
Proof of DIN ISO 9001 certification and listing with well-known OEM’s was the prerequisite for being validated as a supplier to Eckold.
Customers have reported no problems or failures since the implementation of the Neugart gearbox in the clinching systems. Eckold uses the outstanding application knowledge of Neugart contacts in order to detect and remedy irregularities in the overall system. Last but not least, this is supported by the Neugart NCP layout software which is available free of charge to Neugart customers. Each new application at Eckold is designed with this program and subsequently used as part of the technical documentation. Developers then use the Neugart Tec Data Finder to automatically download their specific gearbox as a configured CAD model.
Looking ahead
Even in the reforming and punching technology area, hydraulic and pneumo-hydraulic drives are being replaced with electromechanical drive trains. Eckold supports this market shift with their latest machine types. One challenge for the future will be the option of joining a wide range of new materials using clinching elements. Maintaining machinery with long service lives will continue to be an important criterion for gearbox selection within the industry. All this presents new challenges for the components that are used. Because of the positive experience the company has had, Eckold is highly motivated to strengthen its collaboration with Neugart.
What is clinching?
Clinching, also known as press-joining, is an innovative and proven technique for joining metal sheets and profiles. The permanent joints are exclusively created on the basis of local cold reforming, without additional or ancillary joining components. The main feature of this joining method is that the form-fitting joint is created from the material of the sheets that are being connected.
Because of this, the parts that being joined together can have either the same or different sheet thicknesses and even be made from the same or different materials.
-
Drive systems5 years ago
Intelligent frequency inverters for digital production
-
Industrial Hardware and Machine Parts8 years ago
The necessity of bolted flange connection training
-
Motors8 years ago
New generation of hollow shaft motors
-
Industrial Hardware and Machine Parts8 years ago
ABB and Formula E partner to write the future of e-mobility
-
Industrial Hardware and Machine Parts8 years ago
Rexnord adds to its Autogard Torque Limiters with the XG Series
-
Motors8 years ago
ZF Technology on the Winners’ Podium of the Dakar Rally 2017
-
Gear drives7 years ago
Klingelnberg at control 2018: Tactile and optical measurement on one machine
-
Motors8 years ago
Get a first-class ticket to productivity
-
Motion control7 years ago
Where the robots come from?
-
Motion control8 years ago
Rexnord to Acquire Centa Power Transmission
-
POWER TRANSMISSION TECHNOLOGIES4 years ago
EUROTRANS Board meets for its first session in 2021
-
Industrial Hardware and Machine Parts8 years ago
Custom hobbing tool enables 45-degree angles