Industrial Hardware and Machine Parts
Hexagon displays machine tool innovation
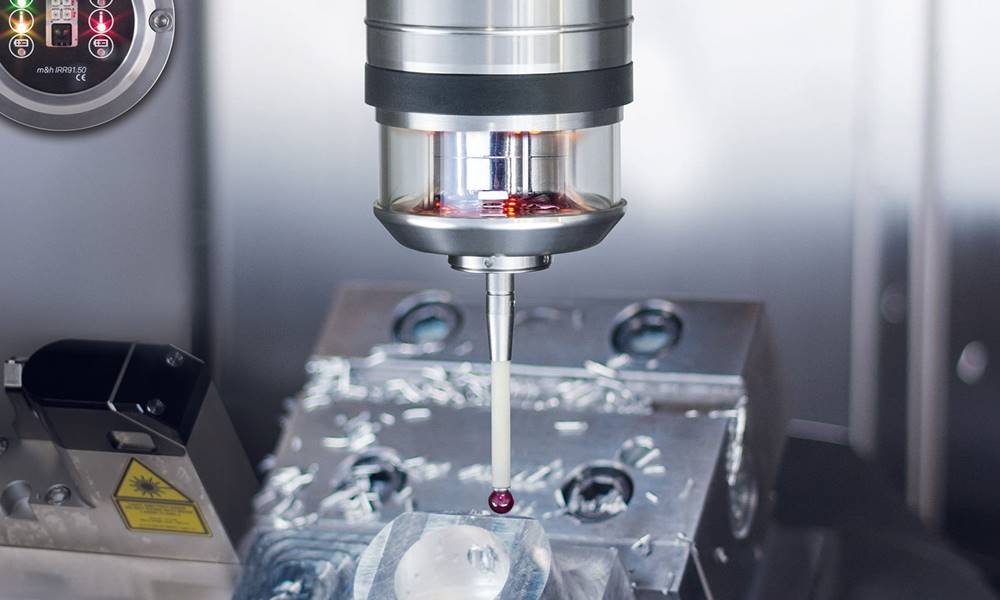
New solutions from Hexagon on display at EMO 2019 deliver faster, accurate, data-rich measurement integrated into the machine tool and a step-change in calibration technology.
Hexagon’s Manufacturing Intelligence division will display at EMO 2019 a range of ground-breaking technologies that address today’s machine tool measurement and calibration challenges while equipping manufacturers to evolve towards Industry 4.0.
Wolfgang Madlener, Product Line Manager Sensors at Hexagon, says: “Hexagon’s ongoing investment in developing smarter manufacturing hardware and software is resulting in innovative products that resolve manufacturers’ current issues and prepare production facilities for the future. For machine tool users this means new ways to more quickly and accurately take measurements on the shop floor and make real-time use of measurement data. Additionally, they can use ground-breaking solutions for calibrating and compensating machine tools.”
Among the innovations on display for the first time will be the LS-C-5.8 laser scanning solution for non-contact surface inspection on the machine tool. It meets customers’ growing demand for an easy-to-use, contactless solution for capturing surface measurement data quickly and directly on the production line. Hexagon is also showing its new ultrasonic touch probe for fully automated thickness measurement, the RWP20.50-G-UTP, which integrates directly with a machine tool. Measuring thickness often requires an elaborate manual setup, which includes the installation of external, manual ultrasonic measuring instruments. Hexagon’s RWP20.50-G-UTP ultrasonic touch probe automates and simplifies the procedure, as part of the machine tool installation, just like a regular touch probe.
EMO 2019 attendees will be able to see Hexagon’s most accurate touch probe for machine tools, the RWP20.50-G-HPP. This radio-wave probe deploys patent-pending laser-triangulation technology inside its measurement unit to achieve extremely high repeatability, low pre-travel variation and low 3D form error. It is ideal for capturing precise measurement results in 2D and 3D and measuring freeform shapes or checking machine kinematics.
The data the LS-C-5.8, the RWP20.50-G-HPP and the RWP20.50-G-UTP capture will be available in real time on the shop floor, enabling manufacturers to quickly identify and address production issues. Data exchange is essential to smarter manufacturing and Hexagon will show how it has optimised the communication capabilities of its latest generation of radio-wave touch probes, with the introduction of the new RWR95.51 radio-wave receiver.
For manufacturers that rely on machining precision in the hundredths of millimetres or even micrometres, Etalon, part of Hexagon’s Manufacturing Intelligence division, has transformed the calibration of small and medium machine tools. The Etalon X-AX LASERBAR delivers a simpler, faster and more accurate way to monitor and calibrate small and medium machine tools and reduce the risk of expensive machining errors. It generates the complete geometrical fingerprint of a 3- to 5-axis machine tool in an automated way in one to two hours, replacing an entire toolbox of conventional calibration equipment for linear and rotary axes.
-
Industrial Hardware and Machine Parts8 years ago
The necessity of bolted flange connection training
-
Drive systems6 years ago
Intelligent frequency inverters for digital production
-
Motors8 years ago
New generation of hollow shaft motors
-
Industrial Hardware and Machine Parts8 years ago
ABB and Formula E partner to write the future of e-mobility
-
Industrial Hardware and Machine Parts8 years ago
Rexnord adds to its Autogard Torque Limiters with the XG Series
-
Motors8 years ago
ZF Technology on the Winners’ Podium of the Dakar Rally 2017
-
Gear drives7 years ago
Klingelnberg at control 2018: Tactile and optical measurement on one machine
-
Motors8 years ago
Get a first-class ticket to productivity
-
Motion control7 years ago
Where the robots come from?
-
Motion control8 years ago
Rexnord to Acquire Centa Power Transmission
-
POWER TRANSMISSION TECHNOLOGIES5 years ago
EUROTRANS Board meets for its first session in 2021
-
Industrial Hardware and Machine Parts9 years ago
Custom hobbing tool enables 45-degree angles