Industrial Hardware and Machine Parts
Is PAT the paradigm-shift that process manufacturing has been looking for?
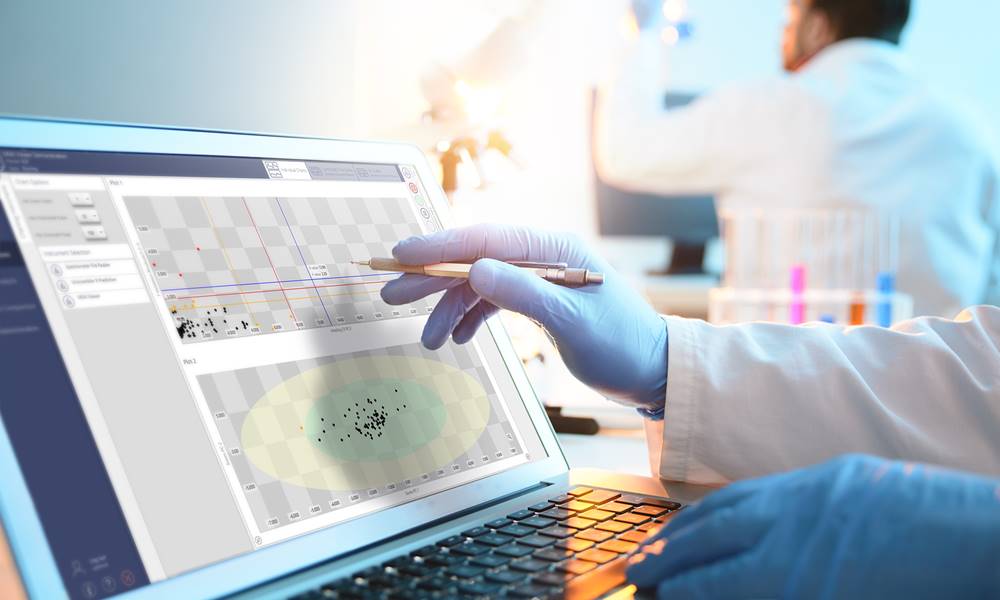
Manufacturers worldwide are taking a closer look at how they can deliver cost-optimised, high-quality products. But will a paradigm shift to real time in-process quality testing allow more manufacturers to embrace the massive cost and productivity benefits available for both batch and continuous production?
Martin Gadsby, Director at Optimal Industrial Technologies, discusses how process analytical technology (PAT) can be a gamechanger in quality management for process manufacturing.
Conventionally, the quality of a batch manufactured product is controlled using manual laboratory testing on samples collected after each unit operation. This is called “Quality by Testing” (QbT). However, traditional quality control has limitations that hinder manufacturing efficiency as QbT takes place too late in the process to prevent scrap and rework. One methodology that has the potential to address this issue is PAT. This provides a real time quality prediction and assurance methodology that enables the process to be continually monitored and optimised, increasing product quality.
By assuring product quality automatically on a live, continuous basis, using multivariate models for instrument calibration, virtually all process manufactured products can be produced far more quickly, more cost effectively and to a higher quality. QbT is no longer required, as timely automated process adjustments can be made to optimise the product quality and reduce or possibly eliminate rework and waste. Using a holistic PAT process model and the right management software, timely measurements of raw and in-process materials can also help contribute to improved process resilience and adaptability.
Why conventional quality control is obsolete
Traditional quality control can often identify issues in the manufacturing process only after the unit operation or batch is finished. In contrast, with PAT-led production the final quality is not tested into the product, but rather built into the product as process adjustments can be made in real-time. It is a “Quality by Design” (QbD) approach. Re-work of sub-standard product batches and wastage caused by the empirically-derived assumption that raw materials are all of a consistent quality is potentially eliminated by adopting a QbD approach. Also, “Real time Release Testing”, where product can be released for sale immediately after production, becomes a reality. The risk of lost sales or direct recall costs and brand damage is also removed.
The role PAT can play in different manufacturing industries
In a highly regulated industry such as biotech and pharmaceuticals, using a PAT based process model means product can be released straight from production into the distribution chain without any further tests or confirmation being required. The significantly reduced development and production time leads to massive savings in production cost and manufacturing time and brings huge advantages in reducing the overhead of Work-In-Progress materials.
The benefits to using PAT for manufacturers of high-value goods are instantly apparent, as any sub-standard batches cause great financial losses due to the large amount of expensive off-spec material produced when things go wrong. Producing lower value product, but at very high speed and in large volumes has the same cost implications in this scenario, so other manufacturing industries such as FMCG can also substantially improve their production processes and reduce losses related to sub-standard products.
Manufacturers of high-volume low-value goods are arguably under more pressure to improve their productivity, speed up production times, reduce rework and scrap while improving the consistency of quality. Real-time QbD processes can also make a difference by allowing bulk producers to use a wider range of potentially lower-cost raw materials, slight variations to in-feed materials can be compensated for with recipe changes that can keep final quality controlled to a much tighter tolerance. PAT is the one technology that has the potential to deliver improvements in all these areas.
Key drivers for PAT-led production
One main concern that may prevent manufacturers from investing in a new technology is whether it is approved by regulatory authorities. In the case of PAT, the shift from testing final batches to building quality into the product is promoted by regulatory bodies that see PAT as a way to foster manufacturing efficiency and product quality, while harmonising regulatory expectations. For example, since the early 2000s both the US Food and Drug Administration (FDA) and the European Medicines Agency (EMA) have promoted the adoption of PAT to support the proliferation of QbD in the pharmaceutical industry.
This holistic approach does however require an effective data and knowledge management tool that allows users to monitor the production critical attributes in real time and enable timely process improvements to optimise quality. Centralised and distributed systems that are designed specifically for PAT, that ensure regulatory compliance and that are helping to drive the PAT revolution are available. One of the most advanced and well-proven PAT data management tools on the market is synTQ, by Optimal. Its market status is underlined by the fact that over half the world’s top-ten global pharmaceutical manufacturers already use it.
At the tipping point of innovation adoption
Industry trends show that manufacturers who have already implemented PAT into their production processes are increasing their market responsiveness, productivity and production capacity whilst also improving the consistency of quality. Other industries are taking note of these successes; thus, the technology is now beginning to gain more widespread acceptance beyond pharmaceutical manufacturers that are effectively the ‘early adopters’. It is now beginning to gain interest among manufacturers of low-volume high-value and high-volume low-value goods. As its visibility increases and the technology matures, its adoption will become ever more widespread to a point where PAT is likely to become an industry standard in many sectors.
-
Industrial Hardware and Machine Parts8 years ago
The necessity of bolted flange connection training
-
Drive systems6 years ago
Intelligent frequency inverters for digital production
-
Motors8 years ago
New generation of hollow shaft motors
-
Industrial Hardware and Machine Parts8 years ago
ABB and Formula E partner to write the future of e-mobility
-
Industrial Hardware and Machine Parts8 years ago
Rexnord adds to its Autogard Torque Limiters with the XG Series
-
Motors8 years ago
ZF Technology on the Winners’ Podium of the Dakar Rally 2017
-
Gear drives7 years ago
Klingelnberg at control 2018: Tactile and optical measurement on one machine
-
Motors8 years ago
Get a first-class ticket to productivity
-
Motion control7 years ago
Where the robots come from?
-
Motion control8 years ago
Rexnord to Acquire Centa Power Transmission
-
POWER TRANSMISSION TECHNOLOGIES5 years ago
EUROTRANS Board meets for its first session in 2021
-
Industrial Hardware and Machine Parts9 years ago
Custom hobbing tool enables 45-degree angles