Fasteners
To gall or not to gall?
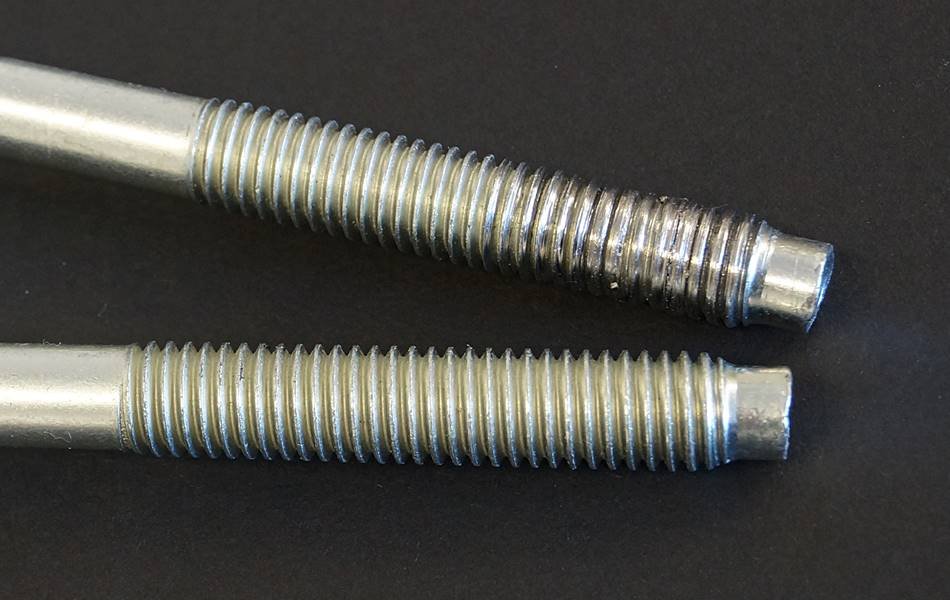
One of the most common problems that occur when tightening fasteners is ‘galling’. While galled fasteners will certainly not be loose, the related joint won’t be properly tensioned and can fail from fatigue when put under service loads. As a result, the equipment may be affected, with mating components being seized, stripped, twisted off or sheared.
Chris Herling, Applications Engineer at Optimas, looks at thread galling and how to reduce its occurrence on the assembly line.
Galling is a form of material wear that occurs when two metal surfaces are in relative motion (e.g. sliding, under load) and their asperities get in contact, generating local stress. This stress disrupts the passive oxide layer over the metals and results in a plastic deformation that generates heat locally, increasing the adhesive attraction. As the movement continues, metallic bonds between the two surfaces are formed, eventually leading to their welding.
When the metal surfaces of nuts and bolts weld together, removal of the fastener will become problematic. In addition, the fastener may be twisted off or have its threads stripped. Therefore, galling can affect the overall quality, reliability and durability of the concerned equipment, even when it only occurs sporadically on the assembly line. This may increase maintenance and repair costs, as the galled or broken fasteners need to be removed and replaced, and the holes where the fasteners are applied may need to be repaired.
If the pro-galling features on fasteners are not eliminated or minimised, they may not only chronically affect the equipment, but the assembly line also, exposing it to recurring inconveniences, such as delays, downtime and occupational hazards.
Design engineers should be aware that certain fastener designs, or environmental conditions, can promote its occurrence. In order to minimise or prevent thread galling, a number of measures can be adopted to choose the optimal design.
Designing for conflicting characteristics
Low surface hardness, rough surface finishes, absence of lubricants, use of fine threaded fasteners or locking fasteners are all factors that can bring on galling. Some of these features may be essential to fastener performance in certain applications. Therefore, it is important to balance the fastener’s properties accordingly.
For example, in corrosive environments, it is necessary to find a balance between anti-corrosion and anti-galling properties, which are both equally affected by surface hardness: while stainless steel, aluminium and titanium don’t easily rust, they are more prone to galling.
Balancing the fasteners’ properties to obtain optimal performance while preventing galling is not an easy task. Highly skilled fastener specialists, such as Optimas, can provide labour-effective solutions that meet the assembly needs. By understanding what is needed, the specialists are able to recognise what features are required and how to combine them. In addition, they can see when standard solutions do not fit with the assembly requirements and act accordingly, modifying pre-existing components or designing and manufacturing new ones.
Another situation where the balancing of a fastener’s characteristics may be required is under conditions of constant vibrations. In this case, thread locking patches are necessary to prevent the fasteners from losing grip over time. The clamp loaded lock also keeps the structure together, preventing it from falling apart and causing major failures. However, the high resistance to vibrations awarded by this solution is caused by an increased friction between the threaded surfaces, which can lead to galling.
How Optimas balanced vibration- and galling-resistance
Balancing vibration endurance and anti-galling properties was a challenge for a Fortune 500 manufacturer of medium- and heavy-duty commercial vehicles. Recurring thread galling issues were experienced on the assembly line when bolting its Diesel Exhaust Fluid (DEF) tanks onto the frame of the truck. While a locking fastener was required to manage the constant vibrations in the system, the overall fastener design did not address galling.
To reduce galling on the assembly line, the manufacturer contacted Optimas. Our expert engineers analysed the bolt straightness, the plating type, and the design and location of the patch, in order to better understand the fastener function, where it was failing and how to optimise it.
As a result, Optimas helped to re-design the fastener. The solution reduced the length of the threaded component, moving from a fully-threaded design to a partially threaded one. Optimas also applied an anti-galling plating and substituted the hard lock patches with soft ones. In addition, Optimas managed the required part’s distribution and logistics to maximise cost-effectiveness. In this way, the manufacturer could not only solve the galling issue, but also significantly reduce the assembly time and increase the number of assemblies realised. This resulted in a more consistent and efficient process, which delivered savings throughout the assembly and product lifecycle.
Master in balancing fastener requirements
Galling is one of the major problem that may occur on bolted joints, causing adhesive wear of the metal surfaces and affecting the tensioning of the system.
It becomes apparent that even the smallest component can rule the effectiveness of an assembly line or cause significant challenges, which in turn may determine the success or failure of a manufacturer. By partnering with experts in engineering and supply, such as Optimas, manufacturers can not only solve incumbent issues such as galling, but also boost safety, quality, speed to market and profitability on their factory floor.

-
Industrial Hardware and Machine Parts8 years ago
The necessity of bolted flange connection training
-
Drive systems6 years ago
Intelligent frequency inverters for digital production
-
Motors8 years ago
New generation of hollow shaft motors
-
Industrial Hardware and Machine Parts8 years ago
ABB and Formula E partner to write the future of e-mobility
-
Industrial Hardware and Machine Parts8 years ago
Rexnord adds to its Autogard Torque Limiters with the XG Series
-
Motors8 years ago
ZF Technology on the Winners’ Podium of the Dakar Rally 2017
-
Gear drives7 years ago
Klingelnberg at control 2018: Tactile and optical measurement on one machine
-
Motors8 years ago
Get a first-class ticket to productivity
-
Motion control7 years ago
Where the robots come from?
-
Motion control8 years ago
Rexnord to Acquire Centa Power Transmission
-
POWER TRANSMISSION TECHNOLOGIES5 years ago
EUROTRANS Board meets for its first session in 2021
-
Industrial Hardware and Machine Parts9 years ago
Custom hobbing tool enables 45-degree angles