Events
Switch to NSK ball screws saves €266,000 a year
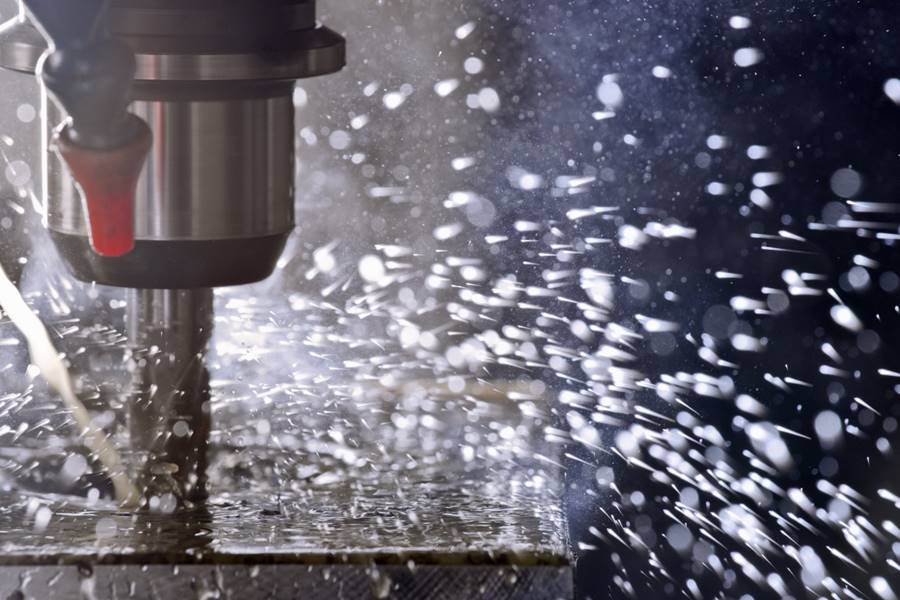
In the framework of the company´s AIP added-value programme, NSK recently helped an automotive component manufacturer to optimise the drive systems in its machining centres, a move that led to six times greater service life and annual savings of approximately €266,000.
High temperatures, coolants, strong forces and high precision:
machine tools make exceptional demands on ball screws.
At a factory in Spain producing automotive brake systems for the global marketplace, some 117 ball screws facilitate linear motion and tool table/changer positioning in a large number of CNC machining centres. However, because of stringent requirements and tough environmental conditions, the ball screws have an average service life of only six months. As a consequence, unscheduled downtimes were causing considerable additional costs to be incurred.
The supplier asked NSK for its expert advice to help to reduce the downtime frequency. In these situations, NSK offers support to customers in the framework of its proven AIP programme. A team of company specialists duly investigated the raceways and lubrication conditions in three faulty linear drives in order to determine failure causes. The result: a combination of high loads, penetrating cutting fluids and high ambient temperatures was responsible for the short lifespan.
To counter these issues, NSK recommended using ball screws that have been specially developed for high speeds and loads. This product range features a customer-specific nut that is tailored exactly to the application and provides greater axial stiffness, not just of the ball screw, but the entire powertrain, thus increasing machine precision. Moreover, as preload is spread over several balls, service life is increased considerably.
As recommended by NSK, the ball screws were equipped with the company´s proprietary X1 high-performance seals. These seals prevent any cutting fluid from penetrating the linear system and stop the ball screw lubricant from contaminating the machining centre’s cutting fluid or coolant. The X1 seal also has excellent grease-retention capabilities.
Optimal lubrication of the ball screw in tough operating conditions is assured by using the K1 lubrication unit, which enables the lubricant’s useful life to be considerably prolonged, again contributing to lower maintenance costs.
On a trial basis, two of the new NSK ball screws were fitted to the machining centres in Spain. The results were highly successful: ball screw lifespan increased by a factor of six. Furthermore, since installation, there have been no more failures.
The automotive supplier can now benefit from lower spare part costs and, above all, from significantly less
production downtime: total yearly cost savings of approximately €266,000 have been achieved.
NSK´s X1 high-performance seal reliably prevents contamination
from penetrating the ball screw.
-
Drive systems5 years ago
Intelligent frequency inverters for digital production
-
Industrial Hardware and Machine Parts8 years ago
The necessity of bolted flange connection training
-
Motors8 years ago
New generation of hollow shaft motors
-
Industrial Hardware and Machine Parts7 years ago
ABB and Formula E partner to write the future of e-mobility
-
Industrial Hardware and Machine Parts7 years ago
Rexnord adds to its Autogard Torque Limiters with the XG Series
-
Motors8 years ago
ZF Technology on the Winners’ Podium of the Dakar Rally 2017
-
Gear drives7 years ago
Klingelnberg at control 2018: Tactile and optical measurement on one machine
-
Motors8 years ago
Get a first-class ticket to productivity
-
Motion control7 years ago
Where the robots come from?
-
Motion control7 years ago
Rexnord to Acquire Centa Power Transmission
-
POWER TRANSMISSION TECHNOLOGIES4 years ago
EUROTRANS Board meets for its first session in 2021
-
Industrial Hardware and Machine Parts8 years ago
Custom hobbing tool enables 45-degree angles