Industrial Hardware and Machine Parts
Custom hobbing tool enables 45-degree angles
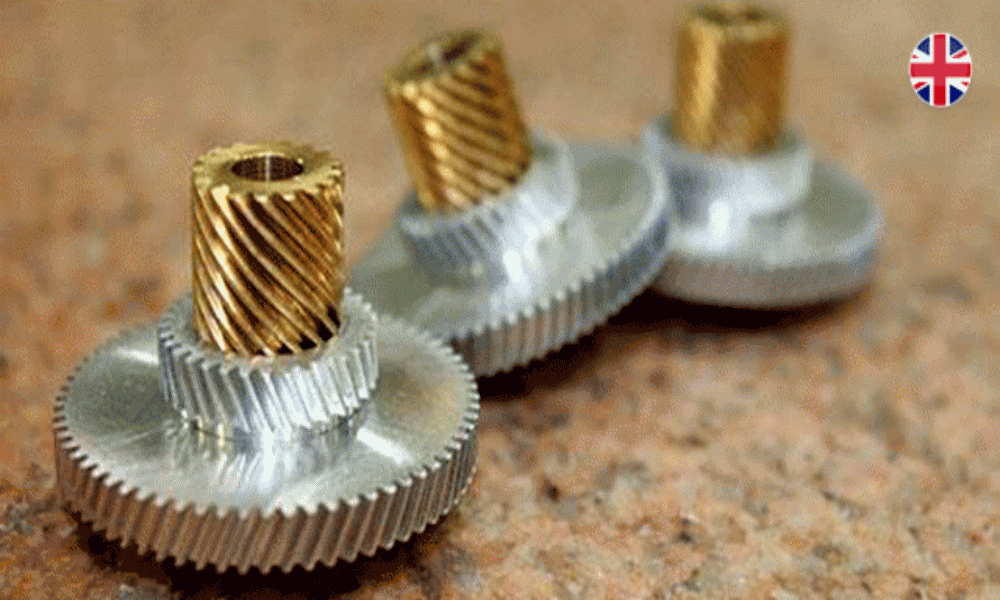
To machine helical gears at 45-degree angles, Gurecky Manufacturing Service Inc. installed a customized multifunctional machine from DMG Mori Ellison Technologies with a hobbing tool from Heimatec.
As the competitive nature within a market increases, so does the need for increased productivity and through put by handling the parts less. One way to meet this need is to accomplish more operations in one setup. Gurecky Manufacturing Services Inc. of Rosenberg, Texas, decided to enhance its manufacturing operations by purchasing a machine that could act as a regular CNC lathe and machine helical gears at the same time. However, a custom hobbing tool from Heimatec Inc. (Prospect Heights, Ill.) was necessary to achieve a desired 45-degree helix angle.
Gurecky was founded in 1983. Today, the company operates out of a 43,000-square-foot facility, serving the oil, gas and energy industries. The company produces multifaceted precision parts ranging from prototypes to mass production. To remain competitive, Gurecky constantly invests in advanced manufacturing equipment. For example, since buying its first DMU 50 ecoline from DMG Mori (Hoffman Estates, Ill.), the company has moved production from traditional vertical machining centers (VMCs) to the more versatile five-axis DMG Mori machines.
In late 2012, Gurecky President John Dorman decided it was time to purchase a CNC machine specifically for gear hobbing. The company approached DMG Mori Ellison Technologies and decided to install its customized multifunctional NLX 2500SY/700 with the ability to hob gears. What made this particular application challenging was the fact that Gurecky needed to machine helical gears at a 45-degree angle. This was a problem because standard hobbing units only allow ±30 degrees of helix angle adjustment due to loss of rigidity.
Undaunted by the task, Heimatec said it could design a custom hobbing tool with ±45 degrees of adjustment to use in conjunction with the new machine. According to Preben Hansen, president of Heimatec, lathes and their coordinating controls are more sophisticated these days, so a dedicated hobbing machine isn’t always necessary. “As long as the machines can handle it, we can build a tool to do it.”
After a few months of testing, the tool was complete and ready to be put to work. Rigidity is the key to tackling this difficult machining operation, he says. “It’s a pretty difficult operation, and when you’re twisting that tool, there’s a lot of leverage. You have to be concerned with the rigidity of the tool. When you’re turning at 45 degrees and milling at the same time, you tend to lose rigidity,” he says.
To combat this loss, Mr. Hansen says Heimatec’s hobbing units are designed with a strong bearing structure. In turn, this structure provides the rigidity necessary to reduce backlash and increase tool life. It also increases the performance of the hobs that do the cutting, he says.

-
Industrial Hardware and Machine Parts8 years ago
The necessity of bolted flange connection training
-
Drive systems6 years ago
Intelligent frequency inverters for digital production
-
Motors8 years ago
New generation of hollow shaft motors
-
Industrial Hardware and Machine Parts8 years ago
ABB and Formula E partner to write the future of e-mobility
-
Industrial Hardware and Machine Parts8 years ago
Rexnord adds to its Autogard Torque Limiters with the XG Series
-
Motors8 years ago
ZF Technology on the Winners’ Podium of the Dakar Rally 2017
-
Gear drives7 years ago
Klingelnberg at control 2018: Tactile and optical measurement on one machine
-
Motors8 years ago
Get a first-class ticket to productivity
-
Motion control7 years ago
Where the robots come from?
-
Motion control8 years ago
Rexnord to Acquire Centa Power Transmission
-
POWER TRANSMISSION TECHNOLOGIES5 years ago
EUROTRANS Board meets for its first session in 2021
-
Motors8 years ago
Interroll introduces a new generation of drum motors