Motors
Servo Motor Alignment Matters: Here’s Why
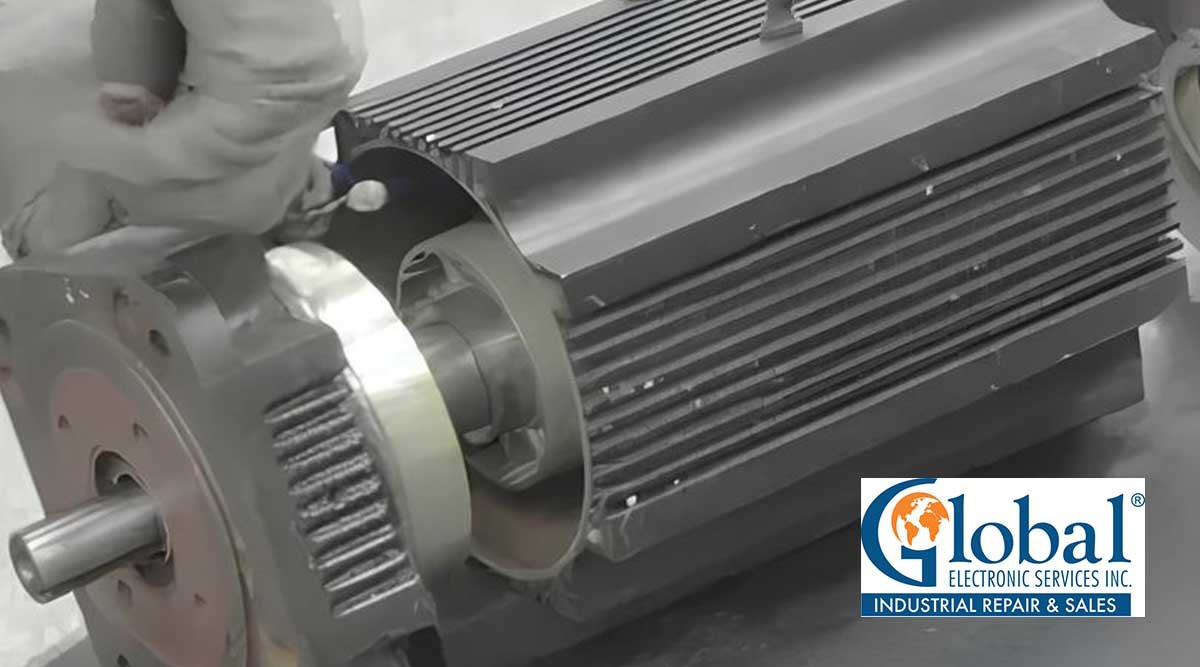
Servo motors are often the core drivers behind automated production lines, CNC machines, and robotic systems. And while they’re powerful tools driving production forward, their effectiveness hinges on proper alignment.
Achieving and maintaining correct alignment isn’t just a matter of good practice — it’s a critical factor in the performance and longevity of your manufacturing equipment. Misalignment, even by fractions of a millimeter, can lead to a cascade of issues that impact your bottom line.
Signs of misalignment — and their consequences
When servo motors are misaligned, the repercussions can be severe and far-reaching. The most immediate impact is a reduction in efficiency and performance. Misalignment forces the motor to work harder to overcome the additional friction and resistance, leading to increased energy consumption and decreased output. Over time, the consequences become more pronounced:
Accelerated wear and tear on bearings, seals, and couplings
Premature failure of motor components
Increased vibration and stress on connected machinery
Higher energy costs due to inefficient operation
Recognizing the signs of misalignment can prevent excessive downtime. Symptoms might be subtle at first, but they can quickly worsen if not addressed promptly. Here’s what to look for:
Unusual vibrations or noise during operation
Excessive heat generation around the motor or coupling
Inconsistent performance or unexpected positioning errors
Increased power consumption without a corresponding increase in output
Proper alignment: Techniques and best practices
Achieving proper servo motor alignment requires precision and the right tools. There are two common methods — both of which GES offers to customers with misaligned servo motors:
Laser alignment: This technique uses lasers to measure misalignment with extreme accuracy. It’s fast, precise, and can detect even minute discrepancies in both angular and parallel misalignment.
Dial indicator method: While more traditional, this method can still be effective when performed correctly. It involves using dial indicators to measure the displacement of the shaft as it rotates.
Maintaining alignment is also an ongoing process. Establish regular inspection and maintenance schedules, and make sure to provide comprehensive training for technicians on alignment techniques. Keep detailed documentation of alignment procedures and measurements for each servo motor and try to regularly analyze performance data to spot potential alignment issues before they become critical.
Servo motor alignment: The benefits
Because servo motors play such an integral role in factory automation, it pays to invest the time and resources in proper alignment. The benefits are manifold:
Improved efficiency and accuracy: Correctly aligned motors operate at peak efficiency, delivering precise movements and consistent performance.
Extended equipment lifespan: Reduced stress on components means less wear and tear, extending the operational life of both the motor and connected machinery.
Lower maintenance costs: Properly aligned systems require less frequent repairs and replacements, reducing both direct maintenance costs and costly downtime.
Enhanced system performance: When all components work in harmony, the entire manufacturing process benefits from improved reliability and output quality.
Keep your servo motors aligned
The importance of servo motor alignment cannot be overstated. It’s a critical factor that impacts everything from day-to-day operational efficiency to long-term equipment reliability and cost management. Well-maintained servo motors lay the foundation for improved productivity, reduced costs, and enhanced competitiveness in the long run.
Now’s the perfect time to have your servo motors serviced, including alignment. Throughout the month of September, GES is running our Servo Motor Special: 15% off three or more servo motor repairs — or 10% off any single repair. Let us restore perfect alignment to your servo motors, so you can reap the benefits of precision automation in your factory!
-
Industrial Hardware and Machine Parts8 years ago
The necessity of bolted flange connection training
-
Drive systems6 years ago
Intelligent frequency inverters for digital production
-
Motors8 years ago
New generation of hollow shaft motors
-
Industrial Hardware and Machine Parts8 years ago
ABB and Formula E partner to write the future of e-mobility
-
Industrial Hardware and Machine Parts8 years ago
Rexnord adds to its Autogard Torque Limiters with the XG Series
-
Motors8 years ago
ZF Technology on the Winners’ Podium of the Dakar Rally 2017
-
Gear drives7 years ago
Klingelnberg at control 2018: Tactile and optical measurement on one machine
-
Motors8 years ago
Get a first-class ticket to productivity
-
Motion control7 years ago
Where the robots come from?
-
Motion control8 years ago
Rexnord to Acquire Centa Power Transmission
-
POWER TRANSMISSION TECHNOLOGIES5 years ago
EUROTRANS Board meets for its first session in 2021
-
Industrial Hardware and Machine Parts9 years ago
Custom hobbing tool enables 45-degree angles